Let in the light. Not the heat. Superior comfort and clarity with 3M™ Sun Control Window Film Prestige Series
- High visible light transmission providing excellent aesthetics
- Up to 97% infrared rejection providing energy savings and enhanced comfort*
- Low interior and exterior reflectivity enhances views while maintaining exterior appearance
- Non-metalized film with no signal interference and no chance for corrosion
- Helps extend the life of furnishings by significantly reducing harmful UV rays, the largest cause of fading
- The Prestige Series can become carbon negative in as short as 6 months from install**
- Comprehensive warranty from 3M
Visible Light Transmission – BEST
Low Reflection – BEST
Infrared Rejection – BEST
Beauty and performance that metallic films can’t match.

Climate Zone 3
Caribe Resort, Orange Beach, Alabama
Customer Issues:
- Protecting furnishings from damaging effects of the sun
- With no change to the exterior appearance of the 14-story building
Approximately 600 square feet of windows installed with Prestige 40 provided improved UV protection for furnishings, heat rejection and low reflectivity.
Product Performance and Technical Data
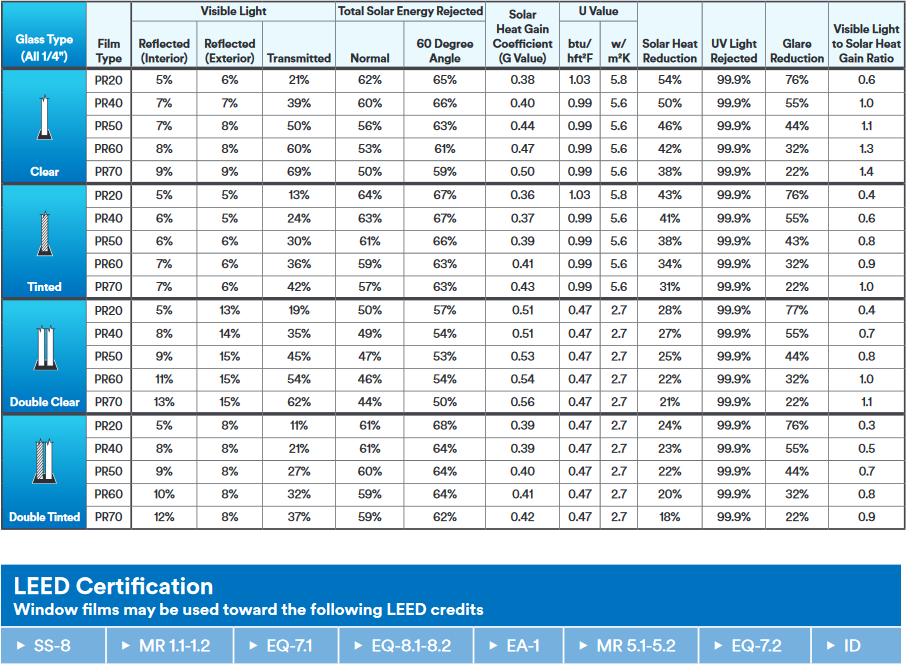
1.1 SECTION INCLUDES
A. Sun control window film. (Prestige)(Ceramic)(Night Vision)(All Season)(Traditional Series)(Exterior Series)
1.2 RELATED SECTIONS
A. Section 08 54 13 -Fiberglass Windows.
B. Section 08 60 00 -Roof Windows and Skylights.
C. Section 08 83 13 -Mirrored Glass Glazing.
D. Section 08 44 23 -Structural Sealant Glazed Curtain Wall.
1.3 REFERENCES
A. ASHRAE -American Society for Heating, Refrigeration, and Air Conditioning Engineers; Handbook of Fundamentals.
B. ASTM International (ASTM):
1. ASTM D 882 -Standard Test Method for Tensile Properties of Thin Plastic Sheeting.
2. ASTM D 412 -Standard Test Methods for Vulcanized Rubber and Thermoplastic Elastomers –Tension.
3. ASTM D 624 -Standard Test Method for Tear Strength of Conventional Vulcanized Rubber and Thermoplastic Elastomers
4. ASTM D 1004 -Standard Test Method for Tear Resistance (Graves Tear) of Plastic Film and Sheeting.
5. ASTM D 1044 -Standard Method of Test for Resistance of Transparent Plastics to Surface Abrasion (Taber Abrader Test).
6. ASTM D 2240 -Standard Method for Rubber Property -Durometer Hardness.
7. ASTM D 2582 -Standard Test Method for Puncture-Propagation Tear Resistance of Plastic Film and Thin Sheeting.
8. ASTM D 5895 -Standard Test Methods for Evaluating Drying or Curing During Film Formation of Organic Coatings Using Mechanical Recorders.
9. ASTM D 4830 -Standard Test Methods for Characterizing Thermoplastic Fabrics Used in Roofing and Waterproofing.
10. ASTM E 84 -Standard Method of Test for Surface Burning Characteristics of Building Materials.
11. ASTM E 308 -Standard Recommended Practice for Spectrophotometry and Description of Color in CIE 1931 System.
12. ASTM E 903 -Standard Methods of Test for Solar Absorbance, Reflectance and Transmittance of Materials Using Integrating Spheres.
1.7 QUALITY ASSURANCE
A. Manufacturer Qualifications: All primary products specified in this section will be supplied by a single manufacturer with a minimum of ten year’s experience.
1. Provide documentation that the adhesive used on the specified films is a Pressure Sensitive Adhesive (PSA).
B. Installer Qualifications: All products listed in this section are to be installed by a single installer with a minimum of five years demonstrated experience in installing products of the same type and scope as specified.
1. Provide documentation that the installer is authorized by the Manufacturer to perform Work specified in this section.
2. Provide a commercial building reference list of 5 properties where the installer has applied window film. This list will include the following information:
a. Name of building.
b. The name and telephone number of a management contact.
c. Type of glass.
d. Type of film.
e. Amount of film installed.
f. Date of completion.
3. Provide a Glass Stress Analysis of the existing glass and proposed glass/film combination as recommended by the film manufacturer.
4. Provide an EFilm application analysis to determine available energy cost reductionand savings.
C. Mock-Up: Provide a mock-up for evaluation of surface preparation techniques and application workmanship.
1. Finish areas designated by Architect.
2. Do not proceed with remaining work until workmanship, color, and sheen are approved by Architect.
3. Refinish mock-up area as required to produce acceptable work.
1.8 DELIVERY, STORAGE, AND HANDLING
A. Store products in manufacturer’s unopened packaging until ready for installation.
B. Store and dispose of hazardous materials, and materials contaminated by hazardous materials, in accordance with requirements of local authorities having jurisdiction.
1.9 PROJECT CONDITIONS
A. Maintain environmental conditions (temperature, humidity, and ventilation) within limits recommended by manufacturer for optimum results. Do not install products under environmental conditions outside manufacturer’s recommended limits.
PART 2 PRODUCTS
2.1 MANUFACTURERS
A. Acceptable Manufacturer: 3M Company, St Paul, Minnesota
B. Point of Contact: Robb Versa, 1-877-684-4040, rob@glassenergy.com
2.2 3M ALL SEASON SUN CONTROL WINDOW FILM
A. Physical Properties:
1. Composition: Optically clear metallized polyester with pressure sensitive adhesive on one side and an abrasion resistant coating on the other.